Swire Beverages Thrives Under Pressure
Swire Beverages is the holding company of Swire Coca-Cola HK Limited, the franchise bottler for all brands of The Coca-Cola Company in Hong Kong. Swire’s extensive brand portfolio offers both carbonated and non-carbonated ready-to-drink beverages. Currently selling approximately 790 million cases in mainland China annually, it’s no surprise that Swire had specific supply chain challenges and needed solutions that could be scaled significantly and provide a fast return.
The phenomenal growth of the Coca-Cola brand in China placed pressure on Swire’s network of bottling production facilities, which were utilizing a manual system that was rapidly reaching a breaking point. In order to handle the accelerated growth of the beverage market in China, Swire needed a solution to manage the forecasted growth of its 10 bottling plants in central, eastern and southern China, as well as the increasing complexity of its products and supply chain. Each of these plants operates relatively independently, but each facility does not manufacture all SKUs that they sell. As a result, additional plants were needed to supply products due to facility capacity restraints.
The company was also faced with more demanding customer service levels, and as a result, its Advanced Planning and Scheduling (APS) center was tapped to provide planning support for a new supply chain joint venture to service all of China’s bottlers, of which Swire is a significant shareholder. The difficulty in accurate forecasting was compounded by the seasonality of the beverage industry, consumer marketing initiatives and the complexity of Swire’s nationwide network.
“Initially the No. 1 challenge was simply how Swire Beverages would cope with the forecasted growth of the business and increasing complexity,” says Maggie Huang, Swire Beverages APS Center director, Supply Chain. “Factor in Swire’s joint venture with Coca-Cola Consolidated, as well as other industry-related opportunities, and we realized the need to implement strategic solutions for Swire to maintain its industry position and to have one synchronized view of demand integrated into all of Swire’s manufacturing, bottling, planning and execution activities.”
Thus, Swire set out to transform its supply chain operations to synchronize with real-time consumer demand across every channel.
Swire based its supply chain improvement program entirely around the teachings of Sun Tzu, circa 500 B.C., in which this famous Chinese scholar advocates the importance of communication, clear procedures, quality of input information and teamwork — all of which are just as relevant today.
Swire selected JDA Software’s supply chain management solutions to better manage its 10 bottling facilities, 47 beverage plants, 75 production lines, more than 280 SKUs, 153 distribution centers (DCs), and 2,700 distributors and logistics partners located across China. JDA Demand helps support Swire’s exponential growth across China with improved forecasting
capabilities and also enables Swire to pinpoint and predict customer demand to maximize sales. Incorporating JDA Collaborate allows Swire’s bottling plants to easily share information over the Internet. JDA Strategy helps strategically plan optimal capacity and sourcing based on costs and constraints across Swire’s entire network.
“JDA Demand enables us to set up the forecasting structure in a three-dimensional hierarchy — by location, by brand and by customer — for all 10 of Swire’s bottling facilities across China,” added Huang.
In addition, JDA Sequencing was implemented at the plant level to optimize materials and resource capacities across each stage of the bottling process, improve plant throughput by reducing changeovers, and perfect the product mix of the individual bottling lines. JDA Fulfillment positions the right inventory in the right DCs, in the right stores and at the right time, while ensuring that inventory is available across the consumer-driven enterprise. Lastly, JDA Monitor allows users to receive early warning of potential problems across the company’s network.
Integrating Swire’s synchronized view of demand into all of its manufacturing and bottling activities has helped it evolve into a more consumer-driven
enterprise. Swire’s clear strategies have resulted in more precise forecasts and supply chain optimization.
Swire effectively managed its exponential growth while also improving or maintaining key supply chain metrics (see sidebar). Consumers benefited from increased product availability because of the reduction in stock-outs and low inventory levels. Swire achieved process compliance across all operations, as well as revenue growth, increased shareholder value and improved operating efficiencies. In fact, since partnering with JDA, Swire Beverages’ sales in China quadrupled.
“Information flow is key to supply chain management. Assisted by information from other IT systems, we can now provide more accurate inventory, sales and order information and consolidate it into the APS system to ensure a smooth flow of information throughout the supply chain. This could not be done without the powerful integration capabilities of JDA’s solutions,” said Huang.
Committed to innovation, Swire continues to fine-tune its supply chain. JDA solutions are currently being used to establish a vendor managed inventory system between Coca-Cola’s non-carbonated supply chain company and Swire that would enable the two companies to share inventories, reduce out-of-stocks and improve supply chain efficiencies. Pilot projects are underway in bottling plants in Guangzhou and Hanzhou.
Swire’s success illustrates the importance of effective supply chain management and demonstrates how the growing Chinese beverage industry is embracing supply chain solutions while still applying local cultural principles.
From the strategy level to the operational level, Swire synchronized its supply chain network, overcame operational challenges and reinforced its leadership position in China’s competitive consumer beverage market.
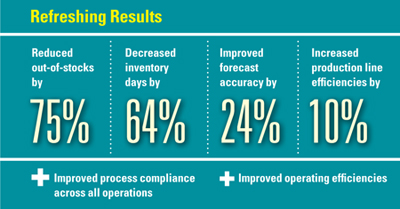
The phenomenal growth of the Coca-Cola brand in China placed pressure on Swire’s network of bottling production facilities, which were utilizing a manual system that was rapidly reaching a breaking point. In order to handle the accelerated growth of the beverage market in China, Swire needed a solution to manage the forecasted growth of its 10 bottling plants in central, eastern and southern China, as well as the increasing complexity of its products and supply chain. Each of these plants operates relatively independently, but each facility does not manufacture all SKUs that they sell. As a result, additional plants were needed to supply products due to facility capacity restraints.
The company was also faced with more demanding customer service levels, and as a result, its Advanced Planning and Scheduling (APS) center was tapped to provide planning support for a new supply chain joint venture to service all of China’s bottlers, of which Swire is a significant shareholder. The difficulty in accurate forecasting was compounded by the seasonality of the beverage industry, consumer marketing initiatives and the complexity of Swire’s nationwide network.
“Initially the No. 1 challenge was simply how Swire Beverages would cope with the forecasted growth of the business and increasing complexity,” says Maggie Huang, Swire Beverages APS Center director, Supply Chain. “Factor in Swire’s joint venture with Coca-Cola Consolidated, as well as other industry-related opportunities, and we realized the need to implement strategic solutions for Swire to maintain its industry position and to have one synchronized view of demand integrated into all of Swire’s manufacturing, bottling, planning and execution activities.”
Thus, Swire set out to transform its supply chain operations to synchronize with real-time consumer demand across every channel.
Swire based its supply chain improvement program entirely around the teachings of Sun Tzu, circa 500 B.C., in which this famous Chinese scholar advocates the importance of communication, clear procedures, quality of input information and teamwork — all of which are just as relevant today.
Swire selected JDA Software’s supply chain management solutions to better manage its 10 bottling facilities, 47 beverage plants, 75 production lines, more than 280 SKUs, 153 distribution centers (DCs), and 2,700 distributors and logistics partners located across China. JDA Demand helps support Swire’s exponential growth across China with improved forecasting
capabilities and also enables Swire to pinpoint and predict customer demand to maximize sales. Incorporating JDA Collaborate allows Swire’s bottling plants to easily share information over the Internet. JDA Strategy helps strategically plan optimal capacity and sourcing based on costs and constraints across Swire’s entire network.
“JDA Demand enables us to set up the forecasting structure in a three-dimensional hierarchy — by location, by brand and by customer — for all 10 of Swire’s bottling facilities across China,” added Huang.
In addition, JDA Sequencing was implemented at the plant level to optimize materials and resource capacities across each stage of the bottling process, improve plant throughput by reducing changeovers, and perfect the product mix of the individual bottling lines. JDA Fulfillment positions the right inventory in the right DCs, in the right stores and at the right time, while ensuring that inventory is available across the consumer-driven enterprise. Lastly, JDA Monitor allows users to receive early warning of potential problems across the company’s network.
Integrating Swire’s synchronized view of demand into all of its manufacturing and bottling activities has helped it evolve into a more consumer-driven
enterprise. Swire’s clear strategies have resulted in more precise forecasts and supply chain optimization.
Swire effectively managed its exponential growth while also improving or maintaining key supply chain metrics (see sidebar). Consumers benefited from increased product availability because of the reduction in stock-outs and low inventory levels. Swire achieved process compliance across all operations, as well as revenue growth, increased shareholder value and improved operating efficiencies. In fact, since partnering with JDA, Swire Beverages’ sales in China quadrupled.
“Information flow is key to supply chain management. Assisted by information from other IT systems, we can now provide more accurate inventory, sales and order information and consolidate it into the APS system to ensure a smooth flow of information throughout the supply chain. This could not be done without the powerful integration capabilities of JDA’s solutions,” said Huang.
Committed to innovation, Swire continues to fine-tune its supply chain. JDA solutions are currently being used to establish a vendor managed inventory system between Coca-Cola’s non-carbonated supply chain company and Swire that would enable the two companies to share inventories, reduce out-of-stocks and improve supply chain efficiencies. Pilot projects are underway in bottling plants in Guangzhou and Hanzhou.
Swire’s success illustrates the importance of effective supply chain management and demonstrates how the growing Chinese beverage industry is embracing supply chain solutions while still applying local cultural principles.
From the strategy level to the operational level, Swire synchronized its supply chain network, overcame operational challenges and reinforced its leadership position in China’s competitive consumer beverage market.
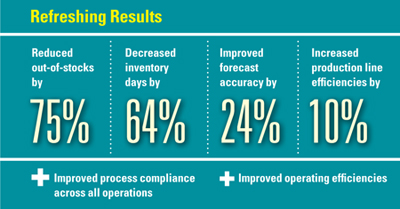