Handle with Care
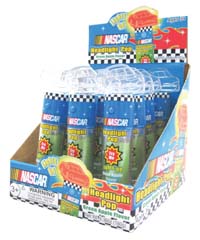
Due to global expansion achieved in the past three years, Kandy Kastle required a complete solution to provide strict management of its logistics process. Most, if not all, of Kandy Kastle's products are delicate in transportation, making effective warehouse storage and transportation important areas of focus. It is also important for Kandy Kastle to manage its supply chain in reverse, in case of damaged products or returns.
In August 2007, Kandy Kastle turned to a supply chain solutions provider to improve the overall logistics process. "We use CaseStack's solution to better automate our process; we currently use MAS 90," says Don Richardson, vice president, sales and marketing for Kandy Kastle. "Implementation was relatively smooth considering the scope of transition."
CaseStack also has the capacity for reverse logistics. For example, if a need such as repair, service, credit or order error arises, the company can utilize this process to move the customers' previously shipped goods from its original destination back to a manufacturer or distribution center.
Since Kandy Kastle's transition to MAS 90, the business has improved its systems tracking, inventory management and overall logistics performance. Richardson says that the solution will "expand with our growth and allow us to offer a high standard of customer service during this growth."