Applica Achieves Peak Performance in Logistics
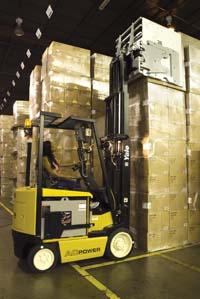
Applica is a marketer and distributor of a wide range of small appliances for use in and outside the home. Applica markets products under licensed brand names such as Black & Decker, company-owned brand names such as Littermaid and Infrawave, and private-label brand names, primarily in North America, Latin America and the Caribbean.
A Time for Change
To effectively service key customers such as Wal-Mart, Target, K-Mart, Sears, Kohl's and Bed Bath & Beyond, Applica has refined and streamlined its supply chain management processes using Infor SCM Warehouse Management Provia (formerly VIAWARE) software.
Prior to the implementation, however, Applica experienced low inventory accuracy, which caused issues with product and location availability and overall order fulfillment.
"The previous system was also not very intuitive or user friendly, so employees and front-line supervisors often struggled with everyday tasks, which also led to general troubleshooting and training issues," says Deanna M. Rainwater, senior director of North America Distribution, who is responsible for leading Applica Consumer Products' North America logistics functions.
After conducting a very thorough due diligence process that included comparing a short list of Tier 1 warehouse management system (WMS) providers and evaluating them against the costs/functionality of upgrading Applica's existing WMS, the decision was made to select Infor. enVista, an implementer of supply chain solutions, was intimately involved throughout the process, including vendor selection in March 2002 and go live four months later.
SCM in Action
The complete SCM solution encompasses Warehouse Management System v. 5.7; a yard management system; a transportation management system (TMS) from FreightLogic; small parcel software from Kewill Clippership; and Oracle Complier from QueriX. It integrates seamlessly with Applica's ERP/OMS system, providing real-time transactional exchanges.
"One of the biggest indicators that an implementation is successful and a system solution is a good fit is gauged by the reaction of the employees on the distribution center floor," says Rainwater. "Applica users responded favorably, the learning curve was short and the trust factor was high."
Here is a snapshot of how Applica uses SCM today:
Tag Tracking of Inventory: Applica has the ability to track individual pallets of inventory through the warehouse lifecycle. It can identify at any given time, in real time, where a pallet of inventory is located in the warehouse from the time that it is received in until it leaves the yard.
Paperless Picking: Wireless RF terminals are used to complete warehouse tasks, allowing real-time updates of inventory moves and transactions.
Transportation Management: A TMS system allows bundling of orders into shipments and least cost routing, resulting in transportation savings. It also provides flexibility to query groups of orders as necessary to support daily operations or special requests.
Yard Management: A yard management system allows a real-time view of carrier equipment on the yard and of inventory loaded in trailers on the yard. It also provides the ability to automatically ship complete (invoice) orders as inventory physically leaves Applica premises.
Small Parcel System: Integration with the small parcel system provides increased throughput of small parcel packages and automates the customer and carrier specific label printing process.
Improved Inventory Location Accuracy: Since implementation, the Little Rock Distribution Center's location accuracy improved from the mid-60 percent range to 98 percent. This eliminated the need for downtime due to physical inventories, and shrinkage is negligible. The system also provided systemic controls that reinforce warehouse best practices to ensure that employees scan and relocate inventory in accordance with standard operating procedures. The solution also provides real-time visibility to track the exact location where inventory is at all times.
Systematically-Configured Quality controls: Ensures that inventory is received one pallet at a time, and each SKU is verified for accuracy as a scanable license plate is attached. Cycle counts are automated to ensure each inventory zone is counted in accordance with the assigned frequency. Each outbound order is 100 percent quality checked through an integrated verification/pallet labeling process. Outbound orders can only be loaded on the assigned equipment and the order/shipment must be loaded in its entirety prior to any bill of ladings being generated. Outbound order status is also available to communicate whether a shipment is currently in a wave, in the process of being picked, staged on the dock or loaded on a trailer.
In an industry where customer satisfaction rules, Applica has a solid supply chain operation platform in place to ensure continued success.
"This system conversion had a quantum leap impact on overall success of the Little Rock Distribution Center by providing a solid operations platform," concludes Rainwater.