Carter's Supply Chain is On the Move
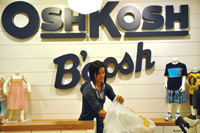
Today, Carter's packs for individual stores and ships multiple SKUs in a single carton. Many of its large customers now have a variety of special requirements for vendors, such as customized labels. They also have private labels, which become competition for Carter's.
Peter Kok, Carter's director of supply chain process development, says, "We are faced with increased complexities and more requirements from our customers who expect us to be just as efficient as they are."
To accommodate new requirements, Carter's had to make modifications to an already highly-customized operating system. Manhattan Associates' Warehouse Management solution, implemented in 2006, resulted in numerous examples of savings and operational efficiencies, including:
- Eliminating the need for repeated customizations
- Being able to maintain "perpetual inventory"
- Improved inventory management and order fill rates
In addition, inventory management is more transparent via piece level tracking. Plus, the transformation of picking and packing as two separate functions into one process streamlined operations.
Additionally, Carter's has been impressed by the solution's flexibility. Peter Kok points out, "It's not a solution that only works if you have a massive operation."
Carter's will continue to increase supply chain efficiency and reliability as well as reduce supply chain costs.
A highly-customized operating system was unable to address Carter's customer requirements efficiently.
"We are constantly working on strategies to lower supply chain costs."
--Mark Paupe, VP of distribution operations, Carter's Inc.